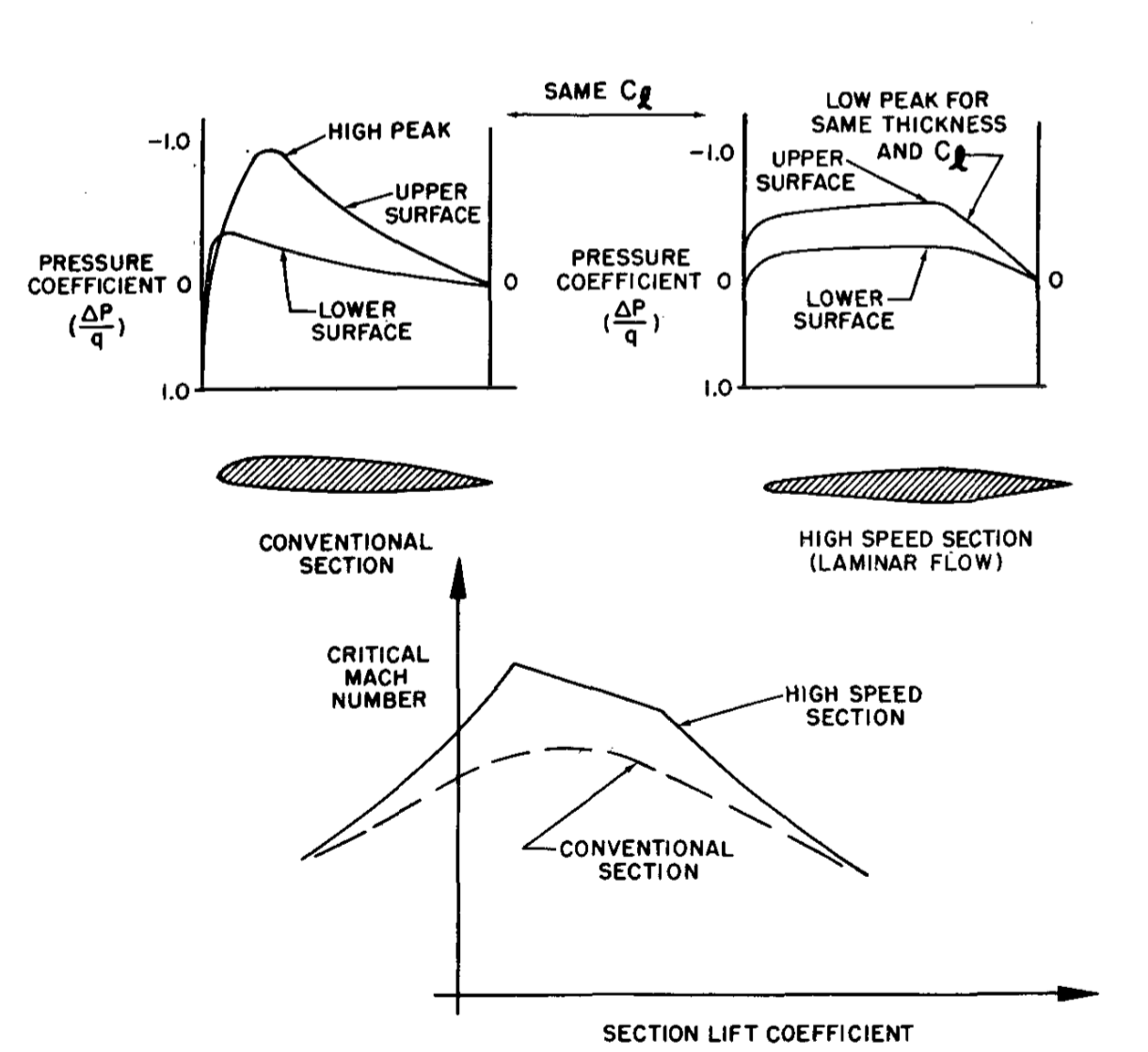
Critical Mach and Airfoil Design
admin@readysettakeoff.com
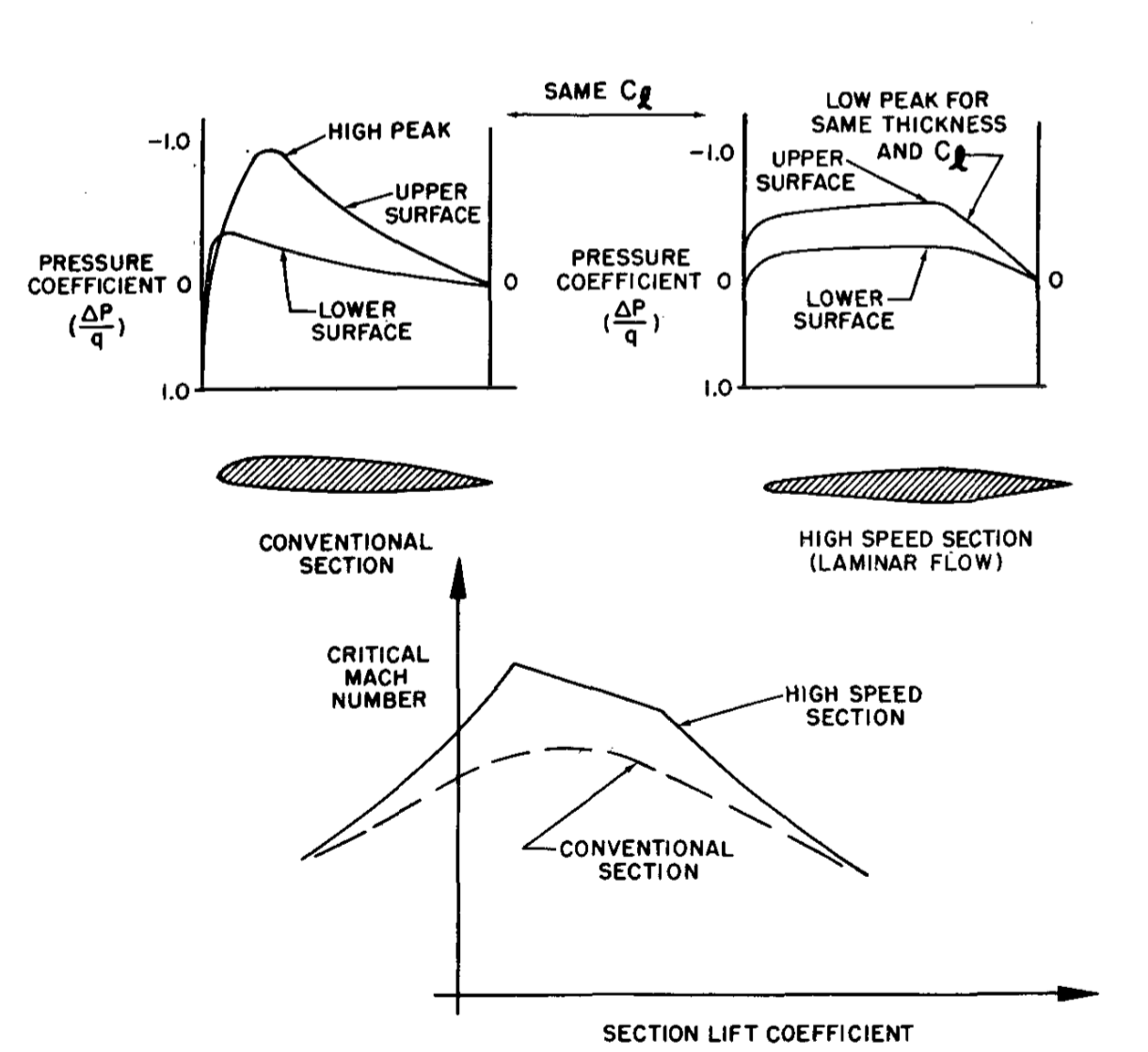
Related Articles
-
Factors Affecting lift
Jet Brain, , Aerodynamics, 0
You are unauthorized to view this page. Please login your credentials Username Password Remember Me Forgot Password
-
Coordinated Turns
Jet Brain, , Aerodynamics, 0
You are unauthorized to view this page. Please login your credentials
-
Basic Aircraft Review
Jet Brain, , Aerodynamics, 0
You are unauthorized to view this page. Please login your credentials
-
Topic of the day: Aerodynamics/Equilibrium
Jet Brain, , Aerodynamics, 0
You are unauthorized to view this page. Please login your credentials
-
Camber Change
Jet Brain, , Aerodynamics, 0
You are unauthorized to view this page. Please login your credentials
-
Longitudinal Static Stability
Jet Brain, , Aerodynamics, 0
You are unauthorized to view this page. Please login your credentials
-
Factors Affecting Lift
Jet Brain, , Aerodynamics, 0
You are unauthorized to view this page. Please login your credentials
-
Airspeed Measurement
Jet Brain, , Aerodynamics, 0
You are unauthorized to view this page. Please login your credentials