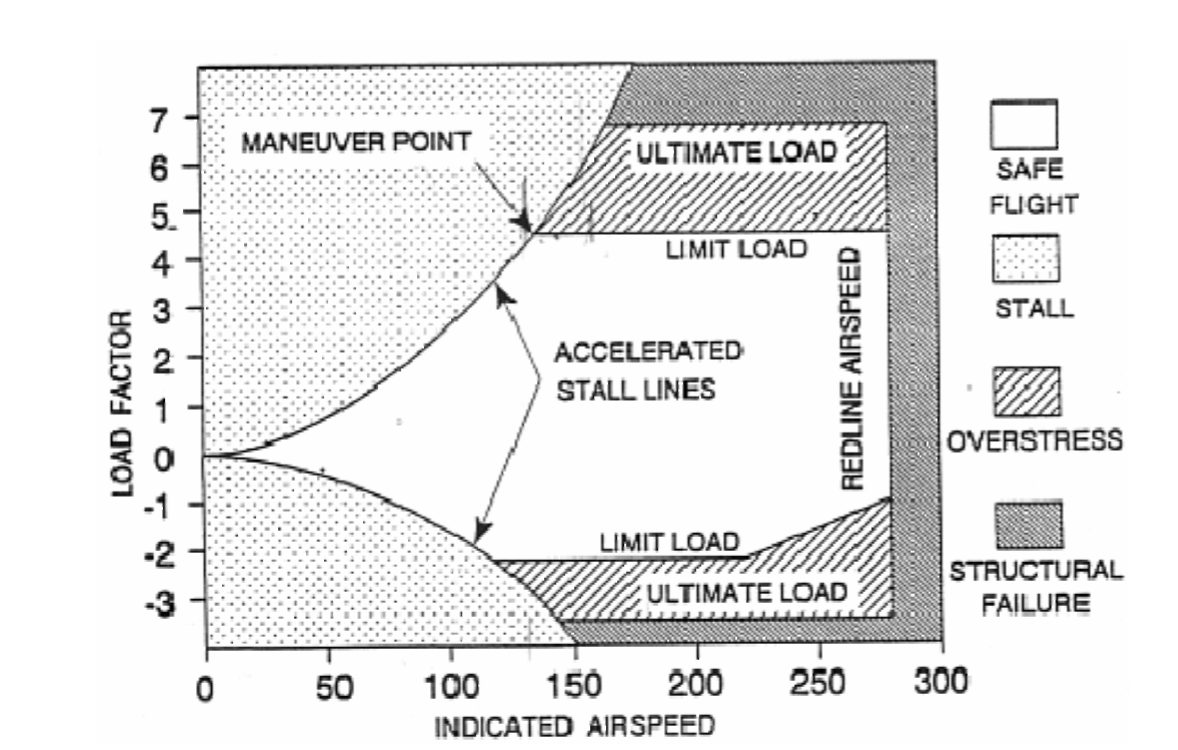
Load Factor
admin@readysettakeoff.com
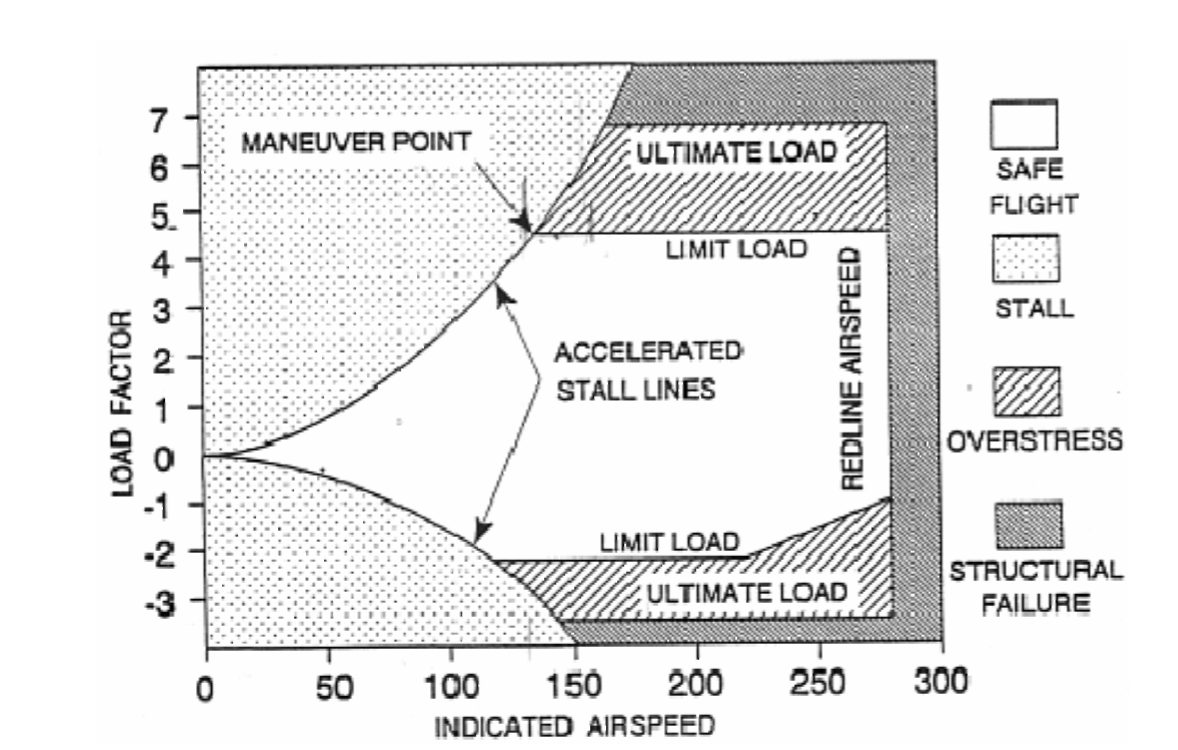
Related Articles
-
Stalls
Jet Brain, , Aerodynamics, 0
You are unauthorized to view this page. Please login your credentials Username Password Remember Me Forgot Password
-
Stability
Jet Brain, , Aerodynamics, 0
You are unauthorized to view this page. Please login your credentials
-
Takeoff Performance
Jet Brain, , Aerodynamics, 0
You are unauthorized to view this page. Please login your credentials
-
Factors Affecting Lift
Jet Brain, , Aerodynamics, 0
You are unauthorized to view this page. Please login your credentials
-
Longitudinal Static Stability
Jet Brain, , Aerodynamics, 0
You are unauthorized to view this page. Please login your credentials
-
Critical Mach and Airfoil Design
Jet Brain, , Aerodynamics, 0
You are unauthorized to view this page. Please login your credentials
-
Wing Dihedral
Jet Brain, , Aerodynamics, 0
You are unauthorized to view this page. Please login your credentials
-
Aerodynamic Balance
Jet Brain, , Aerodynamics, 0
You are unauthorized to view this page. Please login your credentials