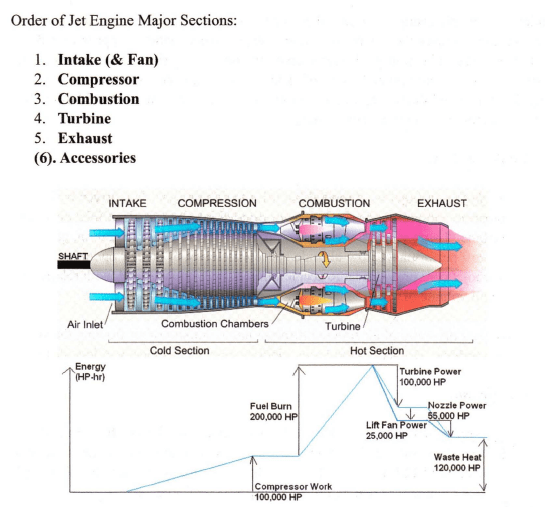
Turbine Engine Review
admin@readysettakeoff.com
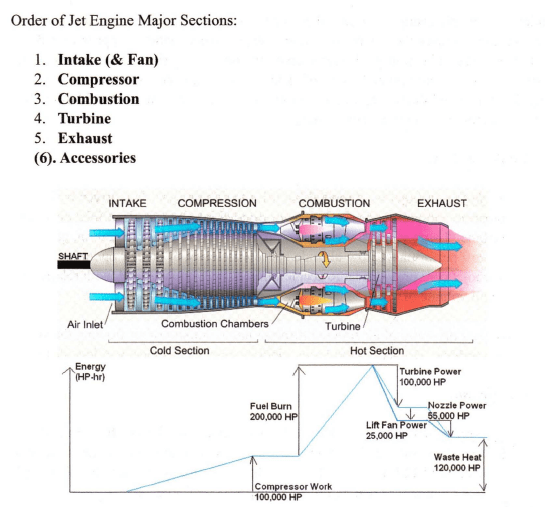
Related Articles
-
Electrical Systems Review
Jet Brain, , Engineering, 0
You are unauthorized to view this page. Please login your credentials Username Password Remember Me Forgot Password
-
Hydraulic Reservoir
Jet Brain, , Engineering, 0
You are unauthorized to view this page. Please login your credentials
-
Electrical Systems Review
Jet Brain, , Engineering, 0
You are unauthorized to view this page. Please login your credentials
-
Turbine Engine/Thrust
Jet Brain, , Engineering, 0
You are unauthorized to view this page. Please login your credentials
-
Thermal Efficiency
rstharold, , Engineering, 0
You are unauthorized to view this page. Please login your credentials
-
Turbine Engine Part 1
rstharold, , Engineering, 0
You are unauthorized to view this page. Please login your credentials
-
Compressor Stall/Surge
Jet Brain, , Engineering, 0
You are unauthorized to view this page. Please login your credentials
-
Turbine Engine Review
Jet Brain, , Engineering, 0
You are unauthorized to view this page. Please login your credentials